Investments
Investments
In 2024, Klabin earmarked R$3.3 billion for investments in operations and expansion projects.
Of the total amount invested, R$845 million was allocated to forestry, up 5% from 2023, mainly due to the addition of forests acquired through the Caetê Project. In addition, R$988 million was assigned to support the operational continuity of plants, 12% more than in 2023, due to the ramp-up of paper machines 27 and 28 at our Ortigueira Plant in Paraná, the startup of our Piracicaba II Plant in São Paulo (part of the Figueira Project) and inflation.
As these outlays are recorded on a cash basis, they do not include investments related to the forest base expansion activities of subsidiaries conducted through special purpose entities (SPEs), which involve contributing existing forest assets already on Klabin’s balance sheet. It is worth noting that there may be a timing mismatch between amounts invested by the Company in such forestry activities and cash inflows from SPE investors.
In 2024, investments in purchases of standing timber and forest expansion totaled R$200 million, down 31% from 2023, due to the acquisition of forestry assets via the Caetê Project.
During the year, R$802 million was earmarked for special projects, up 2% compared to 2023, mainly due to disbursements for the Figueira Project. We allocated R$144 million to the project to modernize our Monte Alegre Plant in Paraná in 2024. Investments in the Puma II Project amounted to R$365 million, down 76% from 2023, due to the start of operations. The Puma II Project has reached the end of its disbursements.
In 2024, R$ 3.4 million were allocated in donations to the state of Rio Grande do Sul, including materials, essential goods, and cash contributions. The total investments in environmental projects amounted to R$213.71 million, while investments in social projects totaled R$28.8 million.
Piracicaba II Plant (SP).
The investments made in the most recent cycle have shown tangible benefits for the Company, putting it in a competitive position:
Puma II Project
Increased production capacity for paperboard and white paperboard, offering Eukaliner® and its variations to the market
Figueira Project
Operational efficiency thanks to state-of-the-art technology and lower conversion costs (box production)
Caetê Project
Reduction in average harvesting radius and the need to buy wood in future; the quality of assets and proximity to the mills will reduce operating CapEx, making the Company more competitive
Caetê Project and New Forestry
Investment in the Caetê Project has proved to be a very successful decision for the Company, leading to a greater reduction in wood production costs than projected. This is the result of integrated work and strong planning.
Without the new assets, given the high demand for raw materials to supply the ramp-up of paper machines 27 and 28 at our Ortigueira Plant, Klabin would have had to source wood from distant areas, mostly acquired from third parties, to supply the mills. While waiting for the acquisition to be approved by the Brazilian Antitrust Regulatory Agency (CADE), the Company drew up an operating plan that considered using Klabin’s raw materials in the first half of the year and the raw material from the new lands in the second half.
Following the conclusion of the land acquisition operation, Klabin began to exploit the new assets, which were of a quality compatible with the Company’s standards. This strategy led to the following results:
Efficiency
The planning work considered the use of Klabin wood in areas closer to the plants and on flatter land, in the first half of 2024.
Savings
There were cost savings of more than R$500 million in terms of harvesting and wood purchases.
Performance of Paper Machine 28
The ramp-up of Paper Machine 28 at our Ortigueira Plant was accompanied by team restructuring, technical improvements to the equipment and strengthened synergies between the operational and commercial teams. Aligned with market demand, the machine was used to produce kraftliner and paperboard. Products were developed and approved by the market, reinforcing the Company’s production capacity. Examples include White Top Liner paperboard, Eukaliner® White 8k and Klamulti®. In 2024, trials were also conducted to produce liquid packaging board, used in beverage packaging.
Attentive to the needs of the paperboard segment, Klabin also started testing a new line of white paperboard, Advance, which can be used in medication, foodservice, candy and fresh milk packaging, for example.
The machine was ramped up to produce kraftliner initially, and as other products were approved, paperboard production was increased while kraftliner production was reduced. Thanks to Paper Machine 28’s flexibility, the Company will be able to adjust its production volumes in the coming years according to market conditions.
MP28 in operation.
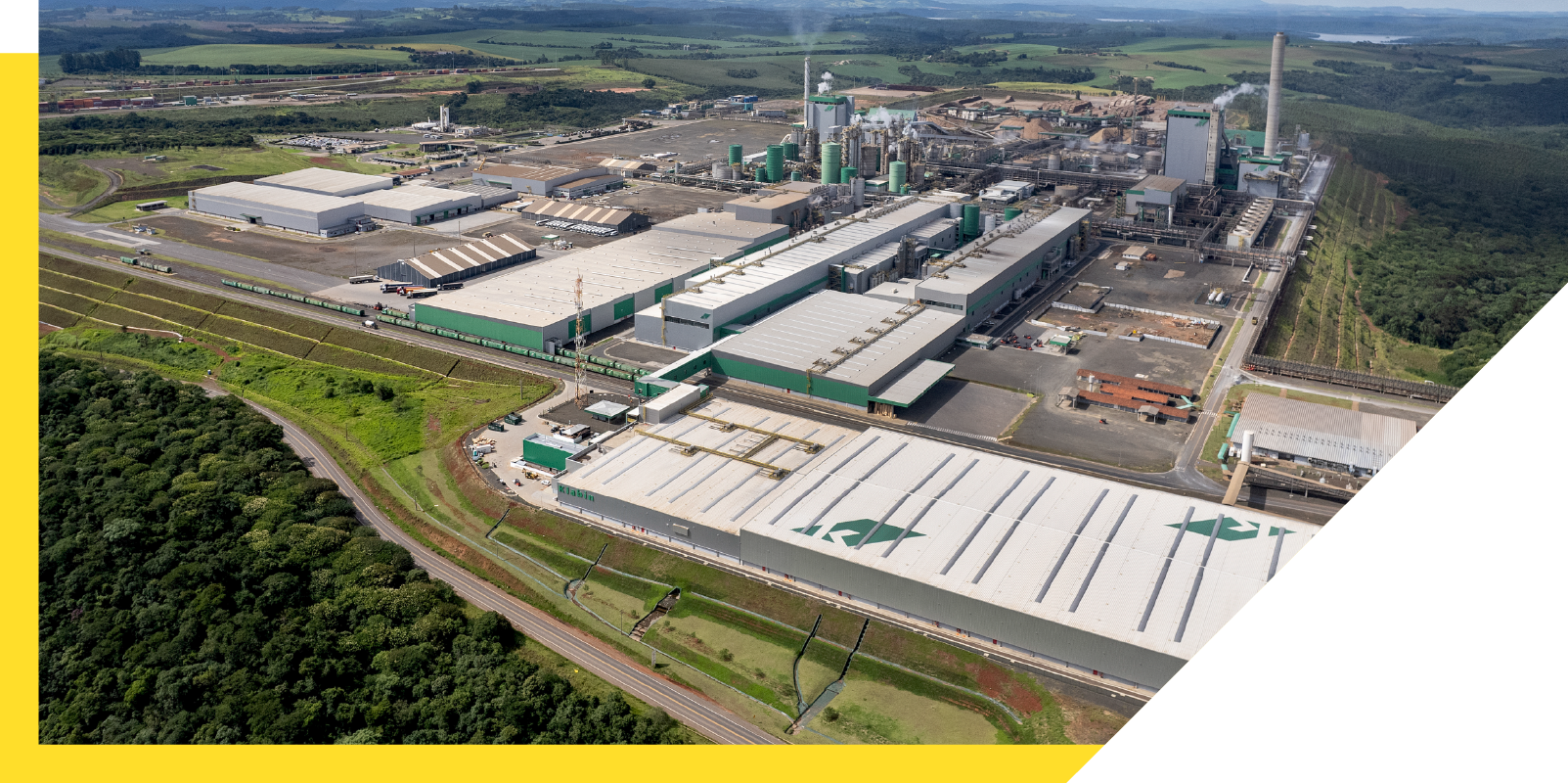
Puma II Project wins award
The Puma II Project, the largest investment in Klabin’s history, won a prize in the 2024 Best and Biggest Brazilian Construction Projects Awards, coming top in the Heavy Industry category. Organized by the Brazilian Engineering Institute and construction news website ConVisão, the awards scheme encompassed 20 categories and assessed the benefits of construction projects for society and their technical and engineering characteristics.
Divided into two stages, the Puma II Project included the installation of paper machines 27 and 28, integrated with fiber production lines, utilities, and chemical recovery systems, as well as infrastructure that enables the use of renewable energy, waste management, effluent treatment, and emissions reduction.
Aerial view of the Ortigueira Plant, home to Paper Machines 27 and 28.
Enhanced efficiency of Piracicaba II Plant
Another investment that has demonstrated its potential is the Piracicaba II Plant (Figueira Project), the largest and most modern corrugated cardboard packaging plant in Brazil. Thanks to it, Klabin will able to meet the additional demand generated by the growth of the corrugated cardboard market and gain market share.
The use of state-of-the-art equipment and the adoption of other innovations, such as vertical storage, mean that the plant’s productivity is almost double that of other plants. Due to its greater production, the plant’s production costs are lower, which brings about financial gains for the Company.
The new plant also posed some challenges. Because of its operational capacity to capture large orders, it was necessary to reassess the dynamics of other plants in Southeastern Brazil to define the product mix for each one. Furthermore, the hiring of labor and the relocation of employees between plants required attention.
Vertical storage at Piracicaba II Plant (SP).
Piracicaba Plant
Modernization of Monte Alegre Plant
The boiler is an essential piece of equipment in the pulp production process, responsible for processing black liquor, a byproduct generated during wood cooking. It enables the recovery of chemicals used in the process and also generates steam at high temperature and pressure. This steam is used to produce renewable energy and, later—at lower temperature and pressure—is reused in process stages that require thermal energy, such as wood cooking, paper drying, and others.
This technological upgrade is expected to yield gains in terms of operational efficiency, cost reduction, sustainability and safety, as follows:
-
Greater thermal efficiency: the equipment can work at higher pressures and temperatures, generating more steam and energy with the same amount of black liquor;
-
More effective control of gas and particulate emissions;
-
Improved collection and treatment of non-condensable gases. Because of the new technology, they will no longer be burned in incinerators, which will be deactivated, as the process will take place inside the boiler itself, reducing perceptions of odors and the use of fossil fuels;
-
Increased energy supplies from renewable sources at the Monte Alegre Plant;
-
Greater reliability, together with reduced safety risks and maintenance costs.
Up to
1,800
new jobs expected during peak construction work
7% reduction* in liquefied petroleum gas consumption,
due to deactivation of incinerators
New boiler expected to start up in the fourth quarter of
2026
* Equivalent to around 5,700 metric tons of LPG per year, which corresponds to an annual emission reduction of 16,700 tCO2
To build the new boiler, preparatory work had to be carried out. The site’s administrative building was removed to make room for the new equipment and a new building was constructed near the factory gate. The new structure began to be used in 2024, leading to gains in well-being and safety for employees.